
For example, you will find aluminum pop rivets with a steel mandrel, which increases clamp loads since the steel mandrel takes more force before it separates from the rivet body. The mandrel isn’t always the same material either. Blind rivets are commonly made from aluminum and steel, but you will also find stainless steel and even plastic composites. Blind rivets are designed as a two-part component with the rivet body and an internal mandrel in the center.

Blind rivets are easily set with one person, greatly reducing installation time, while maintaining the strength of screws, bolts, or even welding, when used in the proper quantity/spacing. If you’re planning an aluminum interior conversion, rear seat delete in your muscle car, firewall bulkhead panel, or other such steel or aluminum work in your project car then rivets will be needed, but which ones and what sizes? Read on.īlind rivets are, for the most part, what are commonly used in automotive applications. Today, rivets are used not only in OEM vehicle manufacturing, but in race car interior and exterior panels, and more.
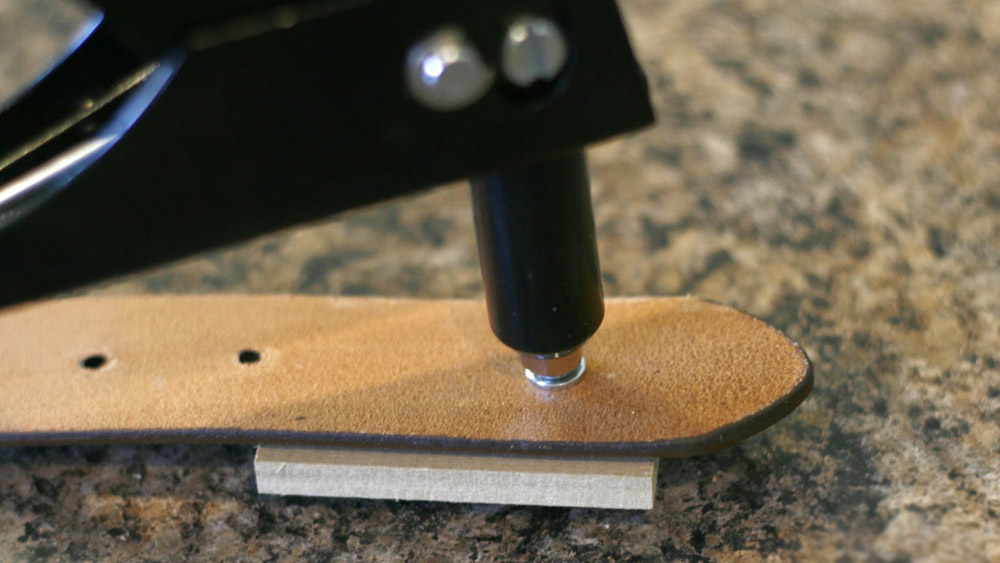
Using rivets in your build saves weight and provides tight panel fitment. They retain two or more components together easily, do not require access to the back side of the work piece, and will not come loose if they are installed properly. This is where a rivet becomes the preferred method of retention. Nuts and bolts work great, if you have access to the back side of the work area and locking fasteners eliminate the worry of loosening, but all those nuts and bolts tend to add a lot of weight. So why use a rivet over a typical nut and bolt or even a tapping screw? For starters, tapping screws rely on the threads and the underside of the screw head for retention and can back out due to vibration not cool at all for your race car let alone a street car.
